Airtightness testing is the recognised method for measuring the extent to which air is lost through leaks in the building fabric. It is often referred to as an air leakage test or air pressure test.
It is important to understand that air leakage is the uncontrolled flow of air through gaps and cracks in the fabric (referred to as infiltration or draughts) and not ventilation, which is the controlled flow of air in and out of the building. Too much air leakage leads to unnecessary heat loss and discomfort for the building’s occupants.
The gaps and cracks within the building fabric are often difficult to detect simply by visual inspection. The most common way of identifying these issues and quantifying infiltration is by a blower door test, which is specified in Part L for new build dwellings. Air permeability is the measure of air leakage and relates an air flow (in m3/hr) to the building envelope. It is expressed in terms of m3/hm2@50Pa. The air change rate relates the air flow to the volume of the building (ach@50Pa).
The building is either pressurised or depressurised to a 50Pa difference to outside conditions using a blower door normally mounted in a door casement. Where required, areas of leakage are then identified either using a thermal imaging camera or smoke.
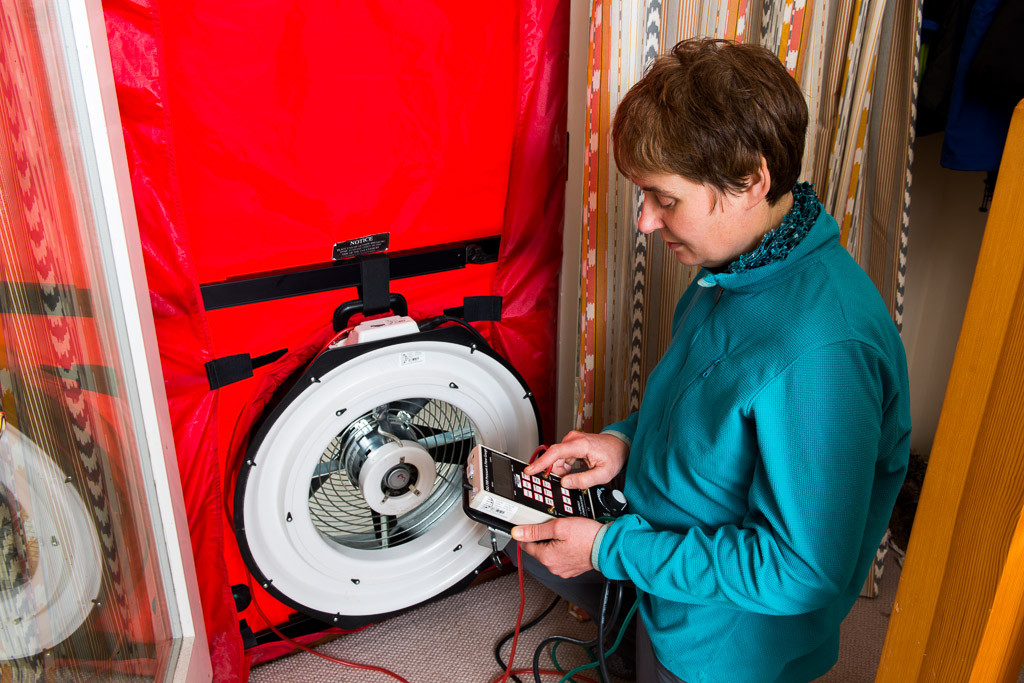
During the testing process, access to the building is severely limited and it should be assumed that it will not be possible for other trades to be working in the property.
For a single new-build property (domestic and non-domestic) to be signed off by Building Control, it is normally expected to have a certified air permeability result lower than the design air permeability (unless other factors on the build have changed). On larger developments, only a percentage of each building type needs to be tested.